Application
Why it is needed:
Corrosion in reinforced concrete structures is the major cause of premature failure of infrastructures like Flyovers, Concrete Bridges, Buildings etc. The most prevalent deterioration mechanism of reinforcement corrosion involves contact of steel with depassivating anions such as chloride & sulphate or the reduction of pH in concrete as a result of carbonation of the cement binder. The crucial characteristic of corrosion mechanism is the hydrated iron oxide compounds formed due to corrosion occupy greater volumes than original reactants (metallic iron).
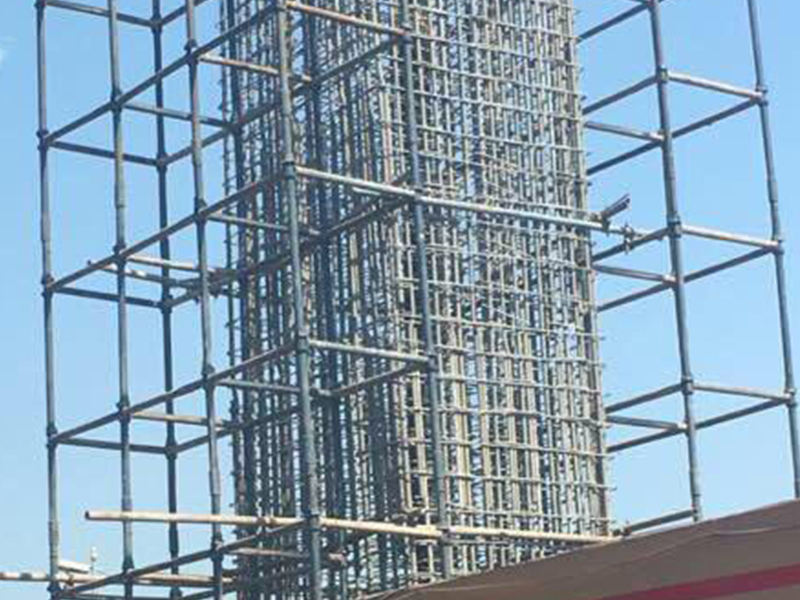
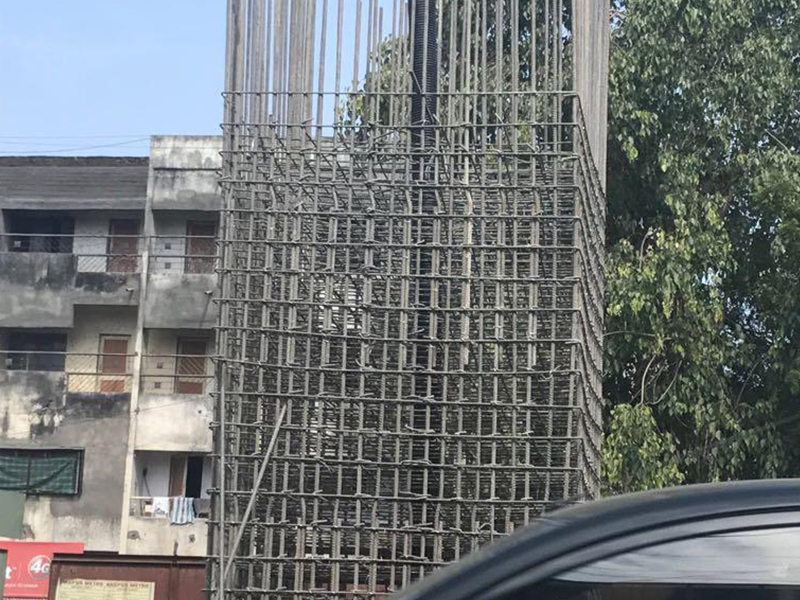
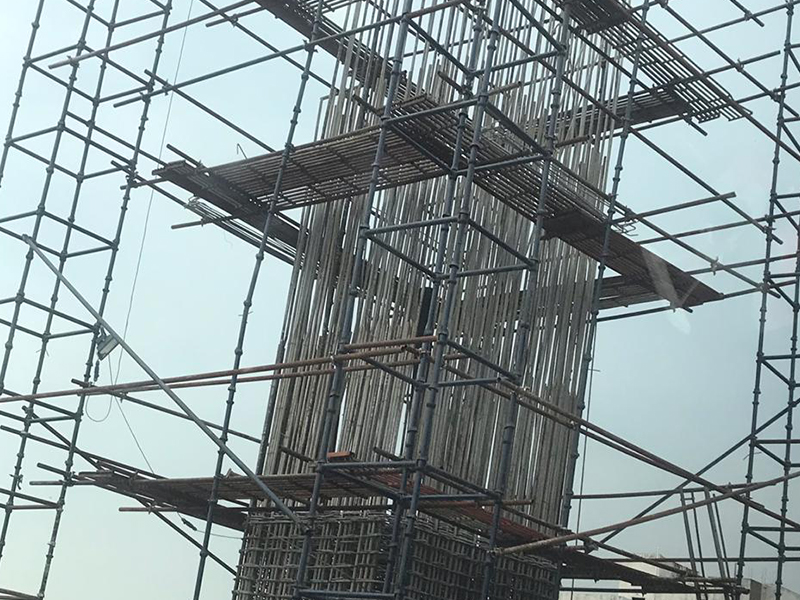
As the volume of accumulated corrosion product increases, pressure is generated within the concrete, which may ultimately exceed the tensile capacity of concrete and result in cracking, delamination and spalling.
Cleanflo Infia private Limited (formerly known as Deioners Speciality Chemicals (P) Ltd.) is the licensee of Central Electrochemical Research institute (CECRI), Karaikudi, Tamilnadu, a National Laboratory affiliated to CSIR, for their process of Inhibitor Solution as per Indian Patent No. 109784/67 that provides protection to reinforcement bars against corrosion.
Method Of Aplication:
Single Steep Treatment (by Inhibitor Solution Only) :
- Manually remove loose rust/iron oxide remnants if any on the rebar by using wire brush.
- The treatment shall be given to the reinforcement only after cutting and bending the same as per the bar bending schedule. Note: If reinforcement bar is to be stored for longer period, then one coat is to be done before bending.
- Make slurry of cement by adding Inhibitor Solution to Ordinary Portland Cement (OPC) in the ratio of 0.5 to 0.6:1 (Theoretical Inhibitor Solution: OPC Cement W/L (weight/liter) ratio basis. No water is to be added while making the slurry or otherwise. The ratio mentioned is for guidelines. However site quantities may vary based on the site conditions for application, ambient weather, skill of manpower, wastage, reinforcement diameter etc.)
- Afterwards apply 1st cost of cement slurry by dipping / brushing/Spraying. Always make the cement slurry in small quantity in a container. Care has to be taken to see that the mix is of uniform consistency. Dipping time for the reinforcement shall enough to cover the entire steel surface with the coating and the area is “bathed” with the slurry. In case of any area left uncoated, the same shall be brushed with sufficient amount of slurry to cover the uncoated area.
- After application of 1st coat of cement slurry keep the bars for drying for 6-12 hours depending on ambient temperature till it is touch dry.
- Repeat the above procedure for the 2nd coat.
- Keep the coated re‐bars for drying on the stacking arrangement.
Note: Always make the slurry in smaller quantities so as to apply them on steels within 2.0 to 2.30 hrs of its preparation as the settling time of cement used in the slurry is 2.0 to 2.30 hrs. This will ensure better bonding of the slurry.
The reinforcement can now be ready for installation and concreting. The entire process time can take between 12-24 hours depending on ambient temperature.
SITE ARRANGEMENT:
- Tank of suitable size is required to treat the reinforcement bar by dipping method .
- Proper Electric Connection / arrangement and Spray Machine required to treat the reinforcement bar by Spraying method .
- Drying platform is required for drying of treated bars.
- Miscellaneous items like bucket, brushes, cotton waste, small weighing balance etc.. are also required at site.
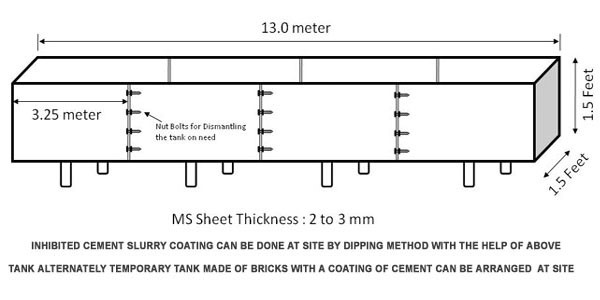
2 Steep Treatment (by Inhibitor Solution & Sealing Solution) :
- As instructed for single steep treatment by Inhibitor Solution after removing lose rust and first coat keep the coated bars for drying for 6-24 hrs on ambient temperature till it is touch dry. After drying use a single coat of Sealing Solution by dipping method (dip it for 1- 2 minutes) or apply by brush, drying time will be 4 hours. (No cement of water to be added).
- Apply Second coat of Cement slurry made with Inhibitor Solution by dipping or brushing method and keep bars for drying for 6-24 hours depending upon ambient temperature till it is touch dry .
- Apply second coat of Sealing Solution by dipping or brushing method (dip it for 1- 2 minutes approx) or apply by brush, drying time will be 4 hours.
Note: Use sealing coat with Sealing Solution for better and long lasting result.
SITE ARRANGEMENT:
- Two number of tank of suitable size is required to treat the reinforcement bar by dipping method for Inhibitor & Sealing Solution separately .
- Proper Electric Connection / arrangement and Spray Machine required to treat the reinforcement bar by Spraying method .
- Drying platform is required for drying of treated bars.
- Miscellaneous items like bucket, brushes, cotton waste, small weighing balance etc.. are also required at site.
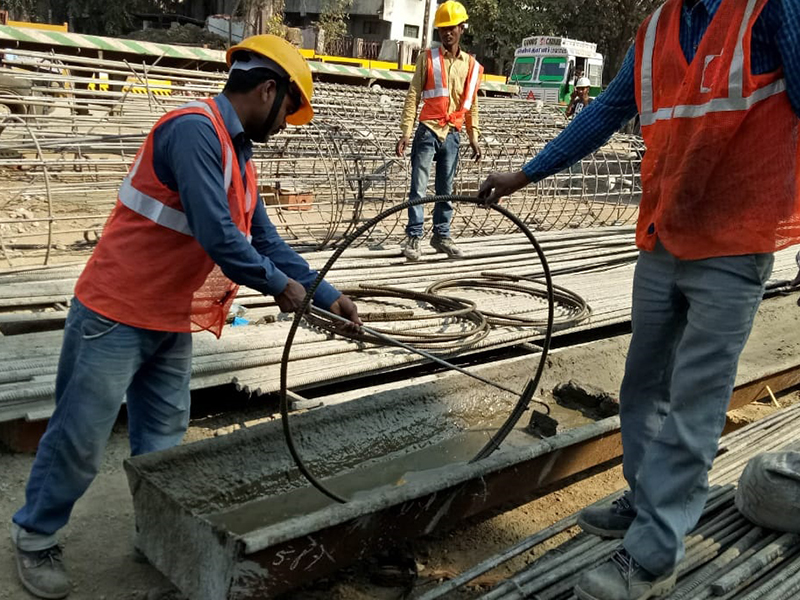
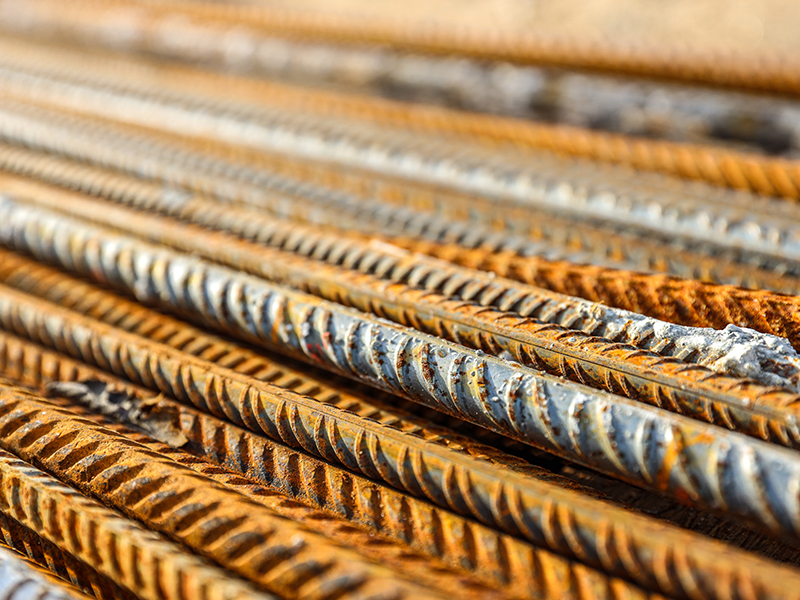
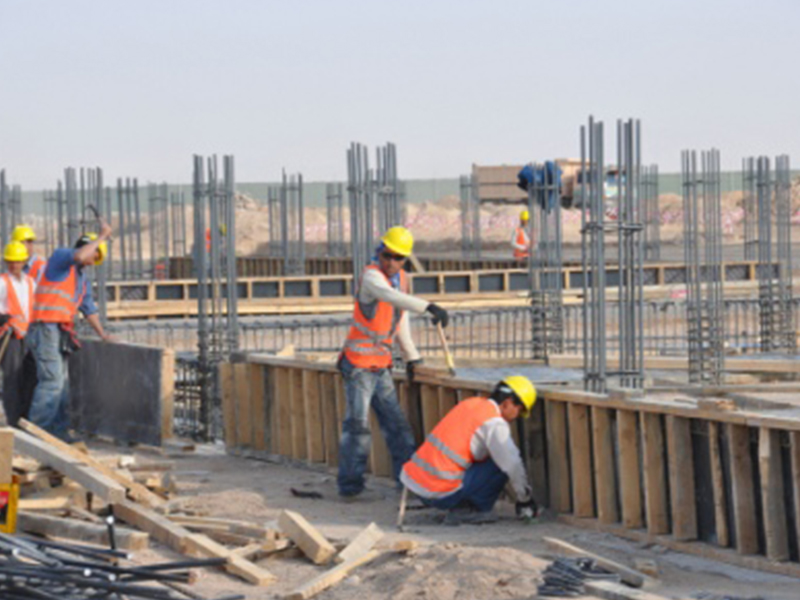
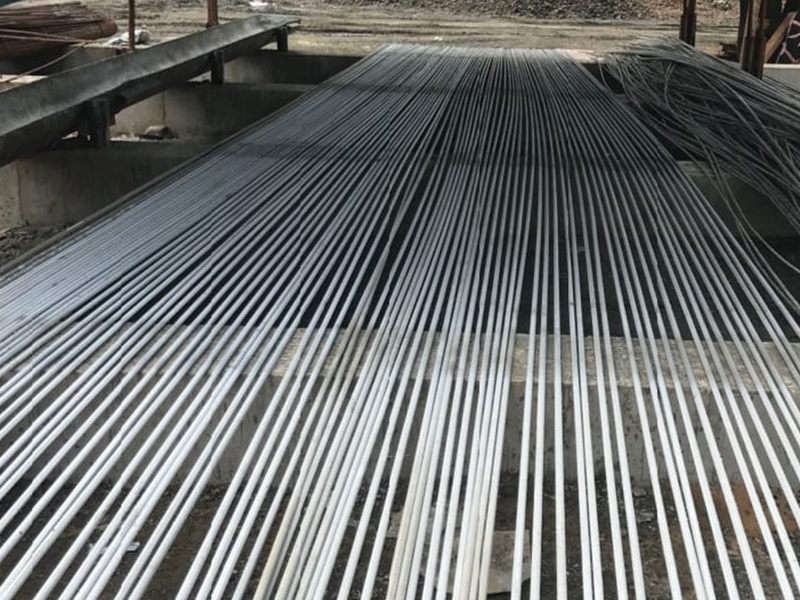
4 Steep Treatment
In saline atmosphere most important thing is to prevent attack Sulphate and Chliride on metal surface. With the adition of the proper Corrosion Inhibitor an alkaline compound be prevented on metal surface.
CHEMICALS:
1. PHOSPHETING JELLY | It is in a slighting yellowish coloured jelly form. Acidic in nature. Indian Patent No: 465/CAL/75 |
2. DE-RUSTING SOLUTION | An inorganic acid with the additives like Acid Inhibitor and Degreasing Agent. Indian Patent No: 109897 |
3. INHIBITOR SOLUTION | Colourless solution containing corrosion inhibitor and alkaline compound. Indian Patent No: 109784/67 |
4. SEALING SOLUTION | Colourless Solution containing silicate base compound. Indian Patent No: 112440/67 |
5. ALKALINE POWDER | White powder. Alkaline in nature. |
THE ENTIRE PROCESS IS BASE ON FOLLOWING SYSTEM:
1) DE RUSTING : Removal of rust, dirt and oil from steel structure.2) PHOSPHETING : Phosphetisation of steel surface (by phospheting jelly) offers temporary protection and prevent rusting by surface conversion process.
3) CEMENT SLURRY : Two coats of cement slurry made by OPC cement and Inhibitor Solution to protect steel surface from the attack of Sulphate and Chloride ions and to keep the steel surface in high pH atmosphere.
4) SEALING : Two coats of Sealing Solution to increase the adhesion between steel and cement coating and to seal the surface and make it impermeable for gracious and water molecules.
THE PROCESS DETAILS:
- The steel rods are to be dipped after cutting and bending into the De-Rusting Solutions for 15-30 min.
- After removal of rusts, the steel bars are to be dipped in Alkaline solution to neutralize the acid remained on the surface of the bars.
- Take out the steel bars from Alkaline Tank and clean with wet cloth.
- Apply the Phospheting Jelly on the entire surface of the steel bars.
- After drying for 30-45 min. the steel bars are again to be cleaned to remove Phosphating Jelly form the surface of the bars.
- After removing the jelly, apply immidiately Inhibitor Solution on the surface of the bar by brush or by dipping.
- After words applying 1st coat of cement slurry by brush.
- After applying the first coat of cement slurry keep the bars for drying for 12 hours.
- After drying period is over 1st coat of Sealing Solution by brush or by dipping.
- Keep drying for 1 hour.
- Apply 2nd coat of cement slurry (same as that of 1st coat.)
- Keep bars for drying for 12 hours.
- After words applying 2nd coat of Sealing Solution on the surface of the bars by brushing.
The treated bars are to be handled and stacked carefully.
This job is completely labor oriented and an individual steel bar is to be handled several times.